PSA Nitrogen Generator Startup Precautions Guide
Proper startup of a PSA nitrogen generator is crucial for its lifespan, nitrogen purity, and production costs. This comprehensive guide covers everything from basic principles to troubleshooting, ensuring optimal performance.
Before starting the equipment, it's vital to check environmental temperature and humidity, ventilation conditions, and the stability of power and air supply. Adjustments to mechanical components, electrical systems, and control parameters are also essential for proper operation. Phased startup and optimized settings allow for gradual equipment stabilization. Regular maintenance and intelligent Operation & Maintenance (O&M) can extend equipment lifespan and improve efficiency.
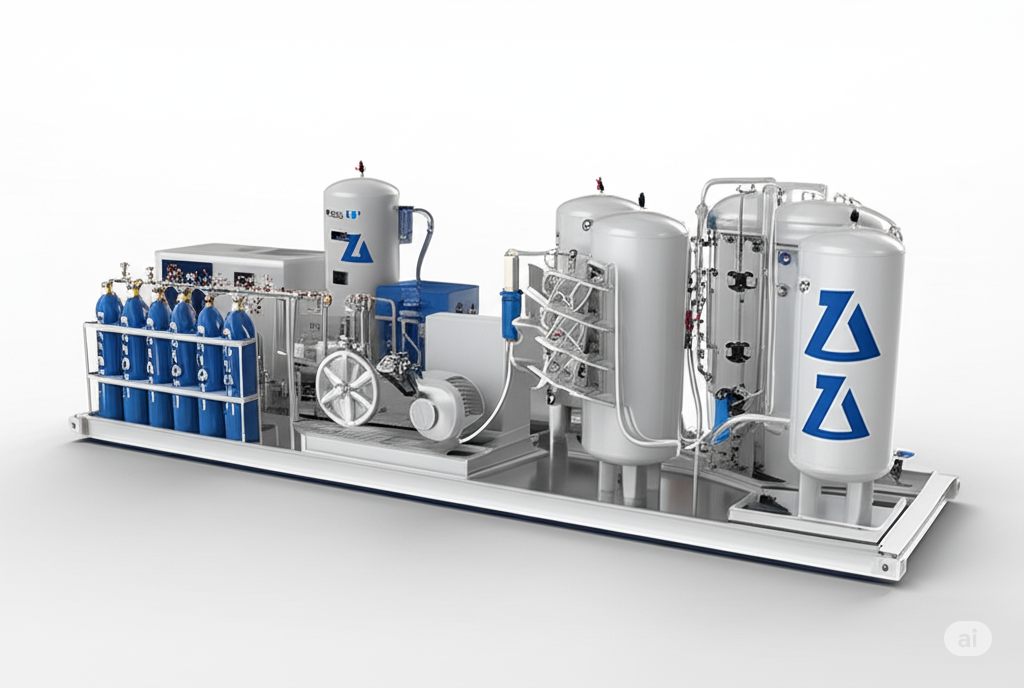
1. Environmental Checks Before Startup
1.1 Ventilation and Temperature-Humidity Control
Key Point: The adsorbent (molecular sieve) in a PSA nitrogen generator is highly sensitive to the working environment; improper temperature and humidity can reduce performance by over 30%.
Ventilation Requirements:
- The equipment should be installed in a dedicated space, away from flammable or explosive gases.
- Minimum ventilation volume should be 1.5 times the air processing capacity of the equipment (e.g., if production capacity is 10Nm³/h, ventilation volume should be ≥15m³/h).
Temperature Specifications:
Item |
Specification |
Note |
Ideal Range |
5 – 40°C |
Best adsorption temperature range for molecular sieves. |
High-Temperature Risks |
Above 45°C |
Adsorption capacity decreases; requires additional cooling devices. |
Low-Temperature Measures |
Below 0°C |
Preheat intake air to above 5°C to prevent pipe freezing. |
Humidity Control:
- Relative humidity should be kept below 80%.
- A dehumidifier is recommended, especially in coastal areas.
Practical Example: In a Southeast Asian food factory, the molecular sieve of an **Allum** generator became clogged due to a workshop humidity of 90%. Installing a cold dryer restored the equipment's gas production efficiency to 95%.
---
1.2 Power Supply and Air Supply Configuration
Power Stability:
Aspect |
Details |
Voltage Matching |
Check equipment nameplate for parameters (e.g., 380V±5%/50Hz). Three-phase unbalance should be less than 2%. |
Grounding Protection |
Ground resistance should be ≤4Ω. An independent grounding pole is recommended (avoid sharing with large motors). |
Lightning Protection |
In areas prone to lightning, a surge protection device (SPD) should be installed. |
Compressed Air Pre-treatment:
Air source quality must strictly follow ISO 8573-1 standards. A three-stage filter installation is recommended:
- **Pre-filter:** Removes particles larger than 1μm (99% filtration efficiency).
- **Activated Carbon Filter:** Oil mist content ≤0.01ppm.
- **Precision Filter:** Residual oil content ≤0.003ppm.
Illustration: Sequence of filters for compressed air treatment.
- **Supply Pressure:** Compressor's output pressure should be ≥0.7MPa, with a fluctuation range of less than ±0.05MPa.
---
2. Equipment Pre-Inspection
2.1 Mechanical Components Inspection Checklist
Valve and Piping System:
- **Confirm Valve Status:** (Check each valve according to the flowchart)
- The intake valve, exhaust valve, and nitrogen outlet valve should initially be in the closed position.
- The drain valve should be manually opened for 10 seconds to remove any accumulated water in the pipes.
- **Leakage Testing:**
- **Soap Solution Test:** Apply soap solution to flanges and threaded connections and check for bubbles.
- **Pressure Hold Test:** Close the outlet valve, pressurize to 0.8MPa, and leave for 30 minutes. The pressure drop should be less than 0.02MPa.
Adsorption Tower and Molecular Sieve:
Aspect |
Verification |
Molecular Sieve Filling Volume |
95% of the tower’s total volume (5% reserved for expansion). |
Powdering Rate Test |
Take a 100g sample and sift through an 80-mesh screen. The remaining powder should be less than 3%. |
Tower Pressure Balance |
Differential pressure between twin towers should be less than 0.01MPa. If higher, check if the equalizing valve is stuck. |
---
2.2 Electrical and Control System Diagnostics
PLC Self-Test Process:
- After powering up, observe whether the touch screen displays the "READY" status.
- Enter the diagnostic menu and check the solenoid valve response time (Normal value: ≤0.1 seconds).
- Verify the accuracy of the pressure sensor (tolerance: ±0.5% FS).
Safety Interlock Test:
- Simulate an overpressure alarm (manually trigger the pressure switch and confirm that the equipment shuts down automatically).
- Test the emergency stop button function.
---
3. Parameter Settings and Phased Startup Strategy
3.1 Core Operating Parameter Setting Guide
Nitrogen Purity and Flow Matching:
Industry Application |
Typical Purity Requirement |
Recommended Adsorption Cycle |
Food Packaging |
99.5% |
60 seconds |
Electronic Component Soldering |
99.999% |
90 seconds |
Chemical Inerting |
99.9% |
75 seconds |
Pressure Control Optimization:
- **Adsorption Pressure:** 0.6 – 0.8MPa (Excessive pressure may cause the molecular sieve to compact, and insufficient pressure affects the gas production rate).
- **Equalization Time:** Set to 15% – 20% of the total cycle time (e.g., for a 120-second cycle, equalization time should be 18 – 24 seconds).
---
3.2 Phased Startup Procedure
Idle Test Phase (30 minutes):
- Turn on the air compressor but do not start the PSA system. Observe pipeline vibrations and noise.
- Record the filter differential pressure (initial value should be <0.05MPa).
Low-Pressure Circulation Test (Set pressure to 0.3MPa):
- Manually switch the adsorption tower 3 – 5 times and check for valve consistency.
- Collect nitrogen purity data and verify control system response.
Illustration: Graph of gradual pressure increase during startup.
Full Load Operation:
- **Step-by-Step Pressure Increase:** Increase by 0.1MPa every 5 minutes until the target pressure is reached.
- **Purity Compliance:** Continuously check for 10 minutes with fluctuations less than ±0.2%.
---
4. Operation Monitoring and Troubleshooting
4.1 Real-Time Monitoring Indicators and Anomaly Thresholds
Monitoring Parameter |
Normal Range |
Alarm Threshold |
Response Measures |
Nitrogen Purity |
Set value ±0.5% |
Below set value by 2% |
Check adsorbent or air source quality |
Adsorption Tower Pressure Difference |
<0.02MPa |
>0.05MPa |
Clean muffler or calibrate sensor |
Cycle Period |
60 – 120 seconds |
<50 seconds |
Adjust equalization time or intake flow |
---
4.2 Common Startup Fault Troubleshooting Manual
Fault 1: Nitrogen Purity Continually Below Standard
- **Possible Causes:**
- Molecular sieve poisoning (oil contamination or water saturation).
- Intake air temperature too high (>45°C).
- **Solutions:**
- Use a dew point meter to detect compressed air moisture content (should be ≤-40°C).
- Disassemble the adsorption tower, sample the molecular sieve, and perform a thermal regeneration test (250°C baking for 2 hours).
Fault 2: System Pressure Fluctuates Significantly
- **Troubleshooting Process:**
- Check if the exhaust muffler is clogged (pressure difference >0.1MPa requires replacement).
- Test solenoid valve coil resistance (Normal value: 22Ω ±10%).
- Calibrate the pressure transmitter (4 – 20mA signal corresponds to 0 – 1MPa).
---
5. Allum Exclusive Optimization Solutions
5.1 Preventive Maintenance Schedule
Maintenance Interval |
Tasks |
Tools and Consumables |
Monthly |
Clean intake filter |
Non-woven fabric for wiping + compressed air backflush |
Every 500 hours |
Molecular sieve replenishment (2 – 3% added) |
13X molecular sieve (1 – 2mm particle size) |
Every 2000 hours |
Replace activated carbon filter cartridge |
Allum original filter cartridge (CF-200) |
---
5.2 Intelligent O&M Upgrade Plan
Remote Monitoring System (Optional):
- Real-time transmission of purity, pressure, and flow data to the Allum cloud platform.
- AI algorithm predicts molecular sieve lifespan (accuracy >90%).
Adaptive Control Module:
- Automatically adjusts adsorption cycles based on gas demand (saving 10 – 15% energy).
---
6. Conclusion
Through detailed pre-checks and timely troubleshooting, the operational stability of the PSA nitrogen generator can be ensured. The optimization solutions provided by **Allum** not only guarantee high-efficiency operation but also reduce equipment maintenance cost and downtime. Implementing best practices and utilizing intelligent solutions is key to ensuring a stable nitrogen supply in various industrial applications.