-
Overview
Programmable Logic Controller, also known as PLC, is a type of industrial computer used to control and automate manufacturing processes, machinery, and other systems. Integrated to modern industrial automation, PLC offers a robust, flexible, and cost-effective solution for industrial automation and control.
Integrated Siemens CPU, Weidmueller connect power, Schneider contactors and breakers and ABB interface relay, Allum's LNS series liquid nitrogen generators' PLC units exhibite unparalleled advantages than competitive products in operation, LN2 generation, liquid level control, working efficiency and reliability.
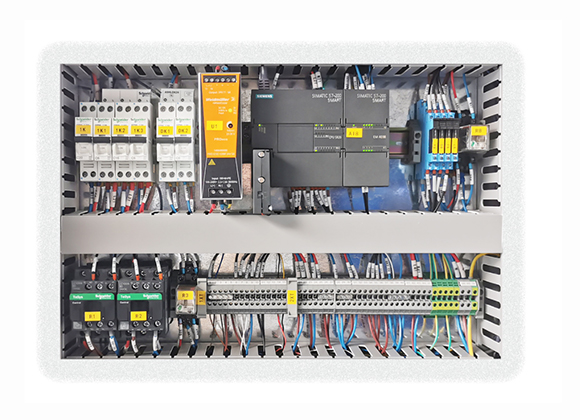
Advantages of PLC
1. Reliability and Durability
Robust Design: PLCs are designed to operate in harsh industrial environments, including extreme temperatures, humidity, dust, and electrical noise.
Long Lifespan: PLCs have a long operational lifespan with minimal maintenance requirements, ensuring continuous operation.
2. Real-Time Operation
Immediate Response: PLCs process inputs and outputs in real-time, providing immediate response to changes in the controlled process.
Consistent Performance: Ensures consistent and precise control of industrial processes.
3. Ease of Maintenance and Troubleshooting
Diagnostic Functions: PLCs come with built-in diagnostics and monitoring tools to detect and report faults, simplifying troubleshooting.
Modular Replacement: Faulty modules can be quickly replaced without affecting the entire system, minimizing downtime.
4. Enhanced Safety
Fail-Safe Mechanisms: PLCs can be programmed with fail-safe operations to ensure safety in case of system faults or failures.
Compliance with Safety Standards: Many PLCs are designed to comply with international safety standards, ensuring they meet regulatory requirements.
5. Data Collection and Monitoring
Data Logging: PLCs can log data from the controlled processes, which can be used for analysis, optimization, and predictive maintenance.
Remote Monitoring: PLCs can be accessed and monitored remotely, allowing for real-time oversight and adjustments.
6. Flexibility and Adaptability
Programmability: PLCs can be easily reprogrammed to handle different tasks, making them highly adaptable to changing production needs.
Modular Structure: Many PLCs have a modular design, allowing for easy expansion or reconfiguration by adding or removing modules.
7. Scalability
Suitable for Various Applications: PLCs can be used in small, medium, and large-scale automation systems, from simple control tasks to complex processes.
Expandable: Additional I/O modules and communication interfaces can be added to meet increasing demands.
8. User-Friendly Programming
Standardized Programming Languages: PLCs use standardized programming languages like Ladder Logic, Function Block Diagram (FBD), and Structured Text (ST), which are relatively easy to learn and use.
Simulation and Testing: Many programming environments offer simulation tools to test and debug the control logic before deploying it to the actual system.
9. Interoperability and Communication
Wide Range of Communication Protocols: PLCs support various communication protocols (e.g., Modbus, Ethernet/IP, PROFINET, DeviceNet) to integrate with other devices and systems.
Network Integration: PLCs can be integrated into larger networked systems, enabling centralized monitoring and control.
Advanced Pulse Tube Cryocooler
-
Overview
Pulse Tube Cryocoolers (PTCs) are advanced, reliable, and efficient systems with unique design, which eliminates moving parts in the cold section, provides significant benefits in terms of durability, low vibration, and noise, making them ideal for sensitive and critical applications.
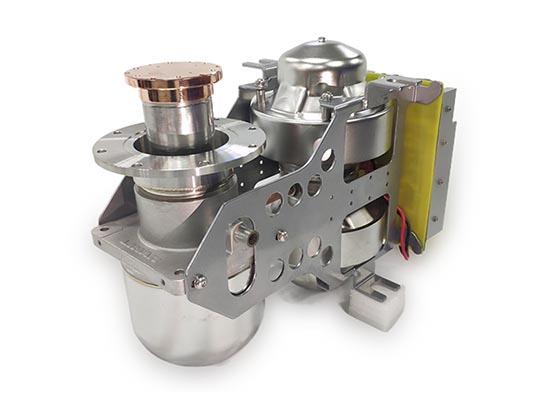
Performance
Pulse Tube Cryocoolers (PTCs) are advanced, reliable, and efficient systems with unique design, which eliminates moving parts in the cold section, provides significant benefits in terms of durability, low vibration, and noise, making them ideal for sensitive and critical applications.
-
Advantages
1. No Moving Parts in the Cold Section:
Reduced Mechanical Wear: Since PTCs have no moving parts in the cold region, there is minimal mechanical wear, leading to increased system reliability and longevity.
Low Maintenance: The absence of moving parts reduces the need for regular maintenance and repairs, lowering operational costs and downtime. Allum's LN2 generators coolers have an expected over 100,000 hours life span.
2. Low Vibration and Noise:
Suitable for Sensitive Applications: The low vibration and noise levels make PTCs ideal for applications that require a stable environment, such as precision instrumentation, infrared detectors, and scientific experiments.
Environmental Benefits: Reduced noise contributes to a quieter and more comfortable working environment.
3. High Reliability:
Long Service Life: The design's inherent reliability ensures a long service life, making PTCs dependable for critical applications.
Stable Operation: High reliability translates to consistent performance with minimal risk of unexpected failures.
4. High Efficiency:
Energy Efficiency: PTCs are designed to optimize heat exchange and thermodynamic efficiency, resulting in a high coefficient of performance (COP).
Energy Savings: The high efficiency of PTCs helps reduce energy consumption, leading to cost savings and a lower environmental footprint.